Avoid Line Disruptions with Schneider Electric's Harmony Range of Pushbuttons
Preventing Downtime: Faulty Pushbutton?
Manufacturing downtime occurs when production stops due to equipment failure, maintenance, or other disruptions, leading to lost productivity and revenue. The less downtime a company has, the more efficient its production becomes. Reducing downtime increases productivity, lowers costs, and decreases accidents.
Importance of Preventing Downtime
Downtime, the enemy of productivity, can cripple operations and result in significant losses. Employing effective maintenance strategies is crucial to mitigate the risk of unexpected breakdowns.
Regardless of the downtime type your organization faces, the objective remains consistent: to diminish overall downtime. Downtime incurs significant costs for a company, encompassing maintenance expenses and production deficits. Unplanned downtime, notably, heightens the risk of workplace injuries and environmental mishaps like unintended fuel spills. Employing suitable technology and analysis tools to reduce downtime can save your organization millions of dollars and weeks of lost production time.
Failure-resistant Product Specifications
Investing in pushbutton technologies with higher reliability ratings, like those rated IP69K and intended for severe environments, can reduce surprise failures. Vendors must demonstrate adherence to endurance standards in their testing laboratories, using aged components. Endorsement by organizations like UL and attainment of necessary worldwide certifications are essential. Devices should be waterproof, operational in wide temperature ranges (-40 °C to 70 °C), and resistant to shock, vibration, and harsh chemicals for longer lifetimes.
Preventive Maintenance Program
End users should replace pushbutton devices proactively, before they reach failure. Vendors should provide indicators of anticipated lifespan, whether through guaranteed operation counts or clear mean time to failure indications in years and months.
With Harmony, you get the tools to optimize your preventive maintenance — Each component’s expected lifetime is specified, expressed in “lambda,” guaranteed number of operations, or mean time to failure.
- These periods are generally much higher than the lifetimes of equipmentor machinery.
- To avoid any loss of business, it is cost effective to replace the most proven elements. By comparing the actual conditions of use of the products to these specifications customers can implement a preventative maintenance of good quality.
This enables end users to establish effective preventative maintenance programs, including provisions for spare parts.
Reactive Organization
To minimize damage during downtime, swift reaction strategies are crucial. Any efforts to reduce the mean time to repair equipment are beneficial. Opt for vendors with widespread global distribution networks, ensuring replacement products are readily accessible near key facilities. Additionally, vendors should offer user-friendly distributor locator tools. When selecting pushbutton units, prioritize both product quality and design to facilitate repairs with minimal spare parts. Products should be configured for quick installation and mounting to minimize operating downtime.
How to optimization maintenance cost with Harmony pushbutton ?
To prevent downtime, we need to improve the equipment. The Harmony range from Schneider is developed and qualified to achieve the highest level of reliability. Harmony range is certified and approved for meeting requirements throughout all continents: EN/IEC, CE marking, UL, CSA, CCC, EAC, JIS, etc., which allows easy exportation of panels and machines using these products in any country around the world. Harmony range also includes emergency stop buttons compliant with higher safety standards, including IEC 60947-5-5.
The modular range Harmony™ diameter 22 can play optimally on three levers:
1. Harmony: The most reliable on the market
The Harmony range is developed and qualified to achieve the highest possible level of reliability. Schneider laboratories use the endurance testing standards and robustness to the harshest industrial environments. Our electrical endurance tests are done after component aging. in offering reinforced waterproof solutions (IP66, 67, 69, and 69K), extending improving this strength, and extending the temperature operating range to -40 °C to 70 °C. These improvements not only allow Harmony to be installed in harsher environments but also guarantee a higher lifetime.
2. Harmony: Tools to optimize your preventive maintenance
Each component’s expected lifetime is specified, expressed in “lambda,” guaranteed number of operations, or mean time to failure. These periods are generally much higher than the lifetimes of equipment or machinery. But if necessary, to avoid any loss of business, it is cost-effective to replace the most proven elements. By comparing the actual conditions of use of the products to these specifications customers can implement a preventative maintenance of good quality.
3. Harmony: limit as much as possible the time to repair your equipment
Schneider Electric and Harmony offer you faultless support in reactive maintenance materials:
Because of its modular design and the wide application market coverage (also recently strengthened by the extension of the waterproofness characteristics, operating temperature range, and the addition of new features such as timer, connectors USB or RJ45, flush mounting kits, etc.), the Harmony range ensures you can repair with a reduced number of spare parts.
At ElectGo, one of Schneider's distributors, you can browse their electronic catalogs and search for everything you need.
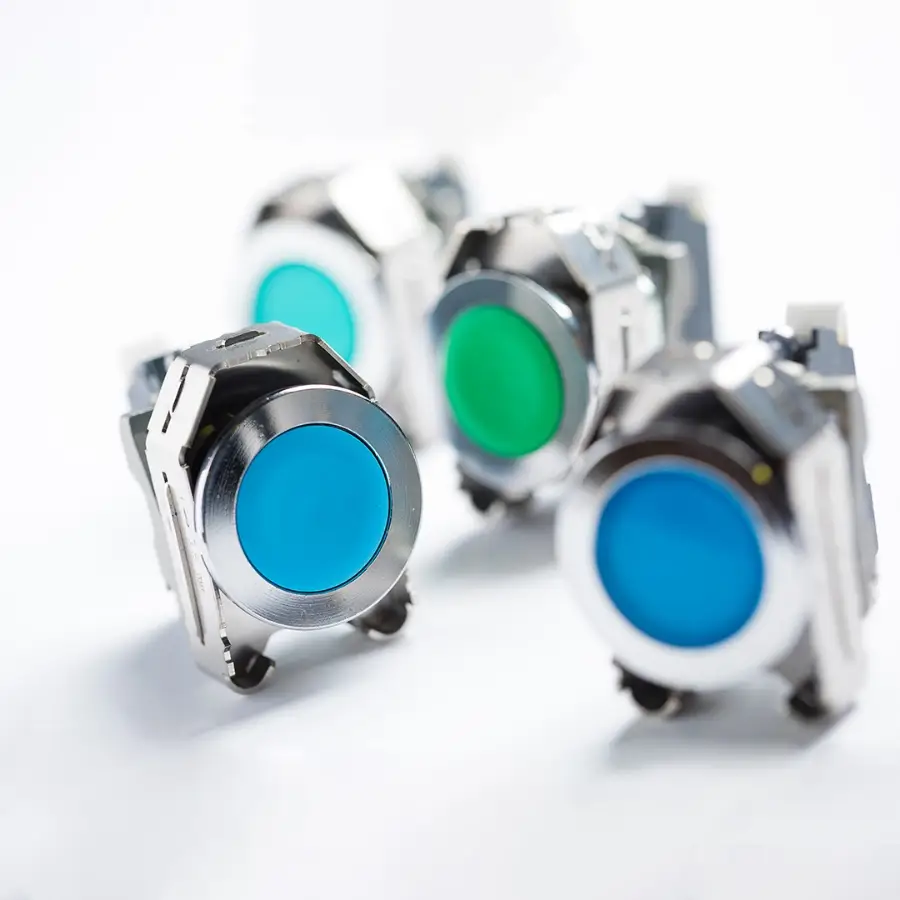
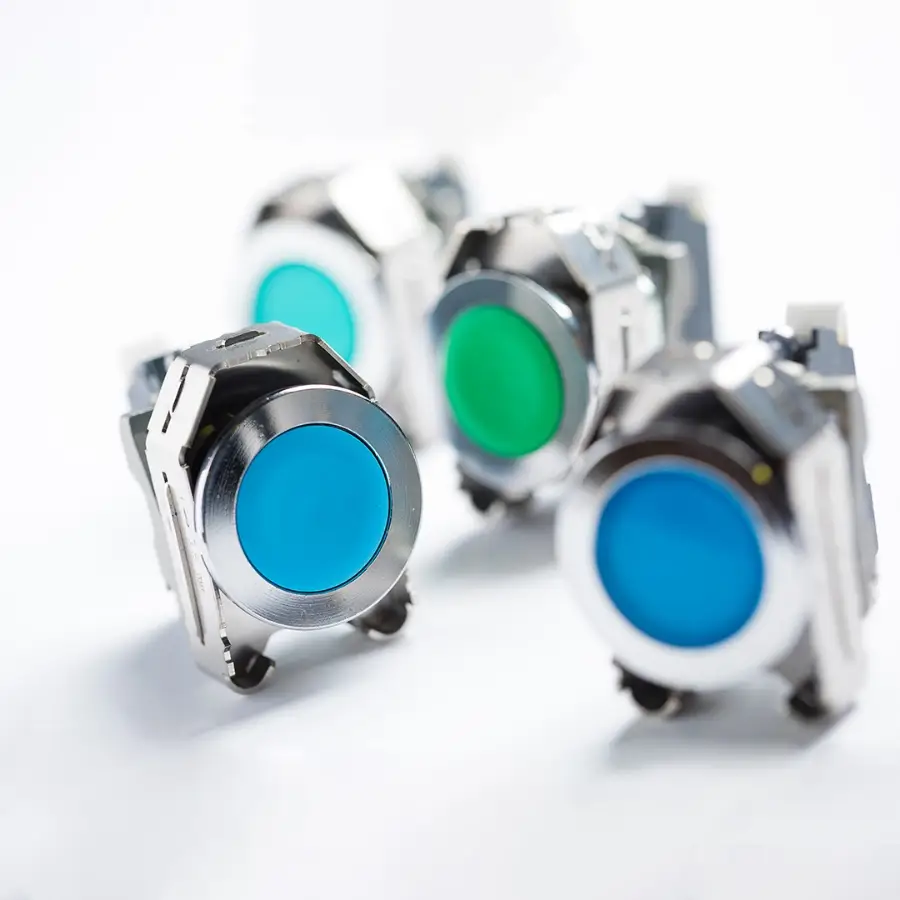
References:
[1] Schneider Electric. (n.d.). Harmony Control Signaling. Available: https://www.se.com/ww/en/work/products/product-launch/harmony-control-signaling/
[2] Schneider Electric. (2017, June 16). Can Industrial Productions Grind to a Complete Halt from a Single Faulty Pushbutton? [Blog post]. Available: https://blog.se.com/industry/machine-and-process-management/2017/06/16/can-industrial-productions-grind-complete-halt-single-faulty-pushbutton/
[3] Schneider Electric. (n.d.). Schneider Electric Harmony™ eXLhoist wireless remote control [Brochure]. Available: https://download.schneider-electric.com/files?p_Doc_Ref=998-19880879_FR-US
[4] Fracttal. (n.d.). Corrective Maintenance vs. Preventive Maintenance. Available: https://www.fracttal.com/en/blog/corrective-maintenance-vs-preventive-maintenance#:~:text=Planning%3A%20Corrective%20maintenance%20requires%20minimal,focus%20on%20prolonging%20asset%20life
Share this article on social media